Share this
Moving from Research to Commercial Production: Lessons Learned
September 25, 2020
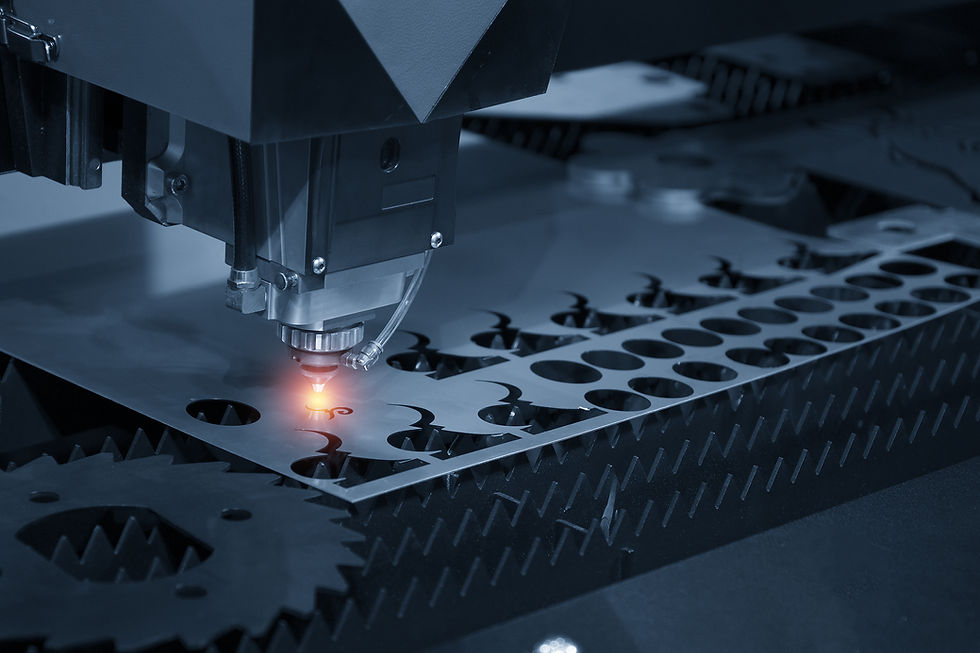
Academic and governmental photonics initiatives fund the laser labs who in turn are able to advance the industry by exploring what is possible without the limits private industry must put on feasibility, operability, and ROI. Laser science, over decades of research, has proven its use in a broad range of commercial applications from laser machining to medical diagnosis and treatment to food inspection to environmental mapping. [Learn more about laser application research]
Yet, despite the many incredible discoveries of potentially useful products, few of these projects ever yield marketable end results. In the move from lab to field, there are several common barriers that would halt commercialization. Some of these include:
Ruggedization
Usability
System integration
Cost targets
Quantum Composers, a designer and manufacturer of photonics equipment, works with its customers from prototype through commercialization of systems. In their experience, they have learned many lessons about the difficulties of moving from design to lab. Their Jewel family of DPSS lasers has yielded one valuable strategy. Mr. Will Bomar, of Quantum Composers, says that they recommend a similar strategy to others in that, “we start with the base laser offering and then allow customers easy ways to fully repackage or customize the laser components to reflect the needs of their unique applications”. He goes on to highlight one recent program in which the Spectrolite laser, originally created for underwater LIDAR, was integrated into a semi-automatic machine used for laser soldering. The unit was adjusted to function on a micron-scale and full automation was critical to usability in the new production environment. This was achieved by:
Small-form package that was easily integrated into the gantry
Laser head that was easy to work with, including camera, laser heat source, and temperature sensor
Complete control of the power level and spot size (10-100 microns), with the ability to define complex temperature profiles providing the flexibility to quickly adapt from job to job
Elimination of water cooling, to remove maintenance concerns and increase reliability in a production environment
Fully microprocessor controlled providing an easy plug & play interface
Costs were maintained by buying in quantity and researching and planning builds to help ensure minimal waste.
In this case, the re-design of the Spectrolite proved to achieve the power and cost targets for this product, while allowing for a system that was easily used in a production environment by multiple technicians. In supporting the customer’s work, Quantum Composers allowed clients to work directly with their product engineers to better understand process parameters and their impact on system performance, ran parallel experiments to improve specifications while meeting cost targets, and throughout prototyping, helped to troubleshoot yield issues to ensure that the overall system design met performance expectations.
Learn more about the Spectrolite or Contact QC to discuss your project
Share this
- photonics (20)
- Lasers (12)
- DPSS Lasers (11)
- pulse delay generator (8)
- pulse generator (8)
- LIDAR (4)
- Laboratory Science (4)
- Lasers and Optics (4)
- PIV (4)
- Technology (4)
- LIBS (3)
- Laser Research (3)
- Nd:YAG Lasers (3)
- Science (3)
- Spectroscopy (3)
- custom laser systems (3)
- laser system (3)
- Aerospace studies (2)
- Commercial Lasers (2)
- Laser Induced Breakdown Spectroscopy (2)
- Laser Science (2)
- Particle Image Velocimetry (2)
- Pulsed Lasers (2)
- custom lasers (2)
- laser ablation (2)
- Biotech (1)
- COVID (1)
- Cancer (1)
- Cancer Diagnostics (1)
- Cancer Research (1)
- Current Generators (1)
- Dentistry (1)
- Emerald Pulse Generator (1)
- Flame Kernel (1)
- High Current Pulse Generator (1)
- Ignition and Combustion (1)
- Ignition flame kernel (1)
- Laser Dentistry (1)
- Laser Manufacturing (1)
- Laser Soldering (1)
- Laser Tooth (1)
- Laser aerospace (1)
- Laser photonics (1)
- MDA (1)
- Mass Spectroscopy (1)
- Micro Soldering (1)
- PIV Laser (1)
- Physics (1)
- Research (1)
- Surface mounted technology (1)
- ablation (1)
- artemis nasa (1)
- blue lasers (1)
- delay generator (1)
- er marketing (1)
- laser attenuator (1)
- laser modules (1)
- laser quality (1)
- laser sales and marketing (1)
- laser synchronizer (1)
- lasers for botanical safety (1)
- lasers for cannabis (1)
- lasers purity (1)
- lasers space (1)
- lunar mission 2021 (1)
- lunar missions (1)
- nasa lasers (1)
- nasa payload (1)
- oem lasers (1)
- photonics sales and marketing (1)
- system synchronizer (1)
- February 2024 (1)
- October 2023 (1)
- December 2022 (1)
- November 2022 (2)
- September 2022 (1)
- July 2022 (1)
- May 2022 (1)
- March 2022 (1)
- January 2022 (1)
- December 2021 (2)
- November 2021 (2)
- September 2021 (1)
- August 2021 (1)
- July 2021 (2)
- June 2021 (1)
- May 2021 (2)
- April 2021 (1)
- March 2021 (3)
- February 2021 (1)
- January 2021 (2)
- December 2020 (1)
- November 2020 (2)
- October 2020 (2)
- September 2020 (4)
- August 2020 (3)
- July 2020 (3)
- June 2020 (4)
- May 2020 (2)
- April 2020 (6)
- March 2020 (3)
- February 2020 (3)
- December 2019 (2)
- November 2019 (3)
- October 2019 (2)
- September 2019 (1)
- August 2019 (2)
- May 2019 (1)
- April 2019 (1)
- February 2019 (1)
- October 2018 (2)
- September 2018 (2)
- August 2018 (2)
- July 2018 (1)
- June 2018 (1)
- April 2018 (1)
- March 2018 (1)
- February 2018 (1)
- January 2018 (1)
- December 2017 (2)
- September 2017 (3)
- July 2017 (2)
- June 2017 (2)
- March 2017 (4)
- January 2017 (2)
- November 2016 (2)
- September 2016 (2)
- August 2016 (1)
- May 2016 (1)
- April 2016 (1)
- March 2016 (2)
- December 2015 (2)
- October 2015 (2)
- September 2015 (1)